Monday, November 28, 2011
Doll Rod
Fixed a nick in the wall low in the shower room. Repainted the shower room wall. Changed the transmission fluid. Made a new 'doll rod' for each fuel tank. Repaired the insulation on the floor boards over the fuel tanks.
Sunday, November 27, 2011
Leather Crotch
Put new rubber washers on the pilothouse ceiling hatch dogs. Replaced missing button on pilothouse bench cushion. Put the stern light back on—it had been removed when the mount for the stern light was elevated earlier this year. Epoxied a leather strip in the crotch of the boom gallows to help protect the boom's Cetol.
Saturday, November 26, 2011
Oxy on Teak Decks
Wash boat. Clean decks with Oxy. Clean bilges. Sealed the wall penetration, caused by the Vacuflush's 1-1/2" hose, between the engine room bilge and the forward bilge. Checked all the flashlight batteries and replaced batteries where necessary. Reconfigured fenders so they can be hung parallel to the water. Washed Phifertex window covers.
Friday, November 11, 2011
Head Hose and Electronics
Installed the new head to vacuum pump hose. Yea! No more vacuum leaks.
Speaking of leaks, the coolant system leak continues to elude me. I found some coolant on the bottom of the overflow bottle. Is it possible that it's the bottle again?
Started installing the Noland RS11. Got both RPM and engine voltage to appear on the Garmins. Need to do some voltage readings while underway to calibrate the pressure and temperature readings.
Installed a temperature sensor on the alternator for the ARS-5 voltage regulator.
Speaking of leaks, the coolant system leak continues to elude me. I found some coolant on the bottom of the overflow bottle. Is it possible that it's the bottle again?
Started installing the Noland RS11. Got both RPM and engine voltage to appear on the Garmins. Need to do some voltage readings while underway to calibrate the pressure and temperature readings.
Installed a temperature sensor on the alternator for the ARS-5 voltage regulator.
Thursday, November 10, 2011
Head Problems...
Removed the 20' of white toilet hose which connects the head to the vacuum pump. I believe it is the source of some of the current head problems.
Wednesday, November 9, 2011
Vacuflush Rebuild
Repaired the leak in the bilge dam. Completely rebuilt the Vacuflush head: all seals, o-rings and valves. Cleaned the teak decks with Oxy detergent. The Oxy does a nice job.
Tuesday, November 8, 2011
Our Singing Head
The Vacuflush head has been making whistling noises like there's either an air or water leak. This morning the head wouldn't flush. Replaced the four duckbills on the vacuum pump. Head flushes fine again. Will have to wait until we're not under way to see if the toilet is still whistling.
Sunday, November 6, 2011
Air In Fuel, Bad
To help find the fuel lines' air leak, a clear length of hose was installed on the fuel supply line, just after the fuel tank selection mainfold. From the presence of air it was obvious that the starboard forward tank was the culprit. Replacing the flared 'L' fitting on the tank eliminated the problem.
The hydraulic steering fill port is now located under the steering station instruments. A simple 3/8" brass plug has replaced the old fill tube and dipstick.
The hydraulic steering fill port is now located under the steering station instruments. A simple 3/8" brass plug has replaced the old fill tube and dipstick.
Sunday, October 30, 2011
Air in Fuel and Coolant in Bilge
On the beginning of Day #11, of our trip from the Chesapeake to Naples, via Miami, Nellie's engine started occasionally changing RPM. While changing all the fuel filters I found the secondary (the one physically attached to the Cummins) filter to be half fuel and half air. The air probably got in while priming the new tanks' fuel lines.
Changed the Cummins' oil and oil filter.
I've been fighting a Cummins coolant leak. The reservoir was losing about 1/4" per 10 hours of running. I could find no leaks around the engine. I now believe the coolant is escaping via the reservoir's cap—I just found it's cracked! The last bottle was replaced because a seam cracked, now this one's cap. We'll know in short order if this is the problem or not.
Changed the Cummins' oil and oil filter.
I've been fighting a Cummins coolant leak. The reservoir was losing about 1/4" per 10 hours of running. I could find no leaks around the engine. I now believe the coolant is escaping via the reservoir's cap—I just found it's cracked! The last bottle was replaced because a seam cracked, now this one's cap. We'll know in short order if this is the problem or not.
Monday, October 24, 2011
New Fuel Tanks Hold 220 Gallons
I just filled three of Nellie's new tanks. The two aft tanks take 55 gallons each, the port forward 65, and starboard forward 45. The port aft was filled last month just after the tanks were installed. Nothing like a 1000 mile sea trial to see if they work--we're five days into a 20 day trip to Miami. I worried about air leaks in the supply lines and so after priming them ran the engine, underway in the Intracoastal, for one hour on each tank. I've now run all four together for 20 hours without incident.
There's a 2" fill port on each inspection plate. I filled via these using a 30 gpm pump—was sure a lot faster. One retrofit will be to cut-off the neck of the fill port which extends several inches into the tank. This makes the last several inches of tank volume slow to fill because the diesel foam can't disperse beyond the fill port. Live and learn.
There's a 2" fill port on each inspection plate. I filled via these using a 30 gpm pump—was sure a lot faster. One retrofit will be to cut-off the neck of the fill port which extends several inches into the tank. This makes the last several inches of tank volume slow to fill because the diesel foam can't disperse beyond the fill port. Live and learn.
Wednesday, October 19, 2011
Picking at Gel Coat
We spent a few more hours picking at Nellie's bottom these last few days. The gel coat that now remains is sticking pretty well. The plan is to put bottom paint on and wait a few years before re-addressing the peeling gel coat. I did find one small blister (dime sized) yesterday on the port side, just aft and 10" below the four through-hulls. The rest of the hull appears to be fine. The bottom was painted with Interlux Micron CSC. The rudder's packing gland and the hose which attaches it to the hull was replaced. This required the rudder to be removed. A new Diver's Dream 6"x12" was installed.
The location of the blister in relation to the port side's most aft thru-hull |
A close-up of the blister |
Tuesday, October 4, 2011
Bottom Repair Thought
4 October 2011
Using picks and paint scrappers we removed all the loose gel coat. As the pictures show a lot came off but there's still a lot of gel coat remaining. The yard is proposing to remove the gel coat mechanically. Unfortunately the shaving process will also take off as much as an 1/8" of fiberglass. This is a technique common in the repair of blistered bottoms. Since there are no blisters on Nellie, removing fiberglass is drastic and unwarranted. I continue to believe the best course of action is to let the gel coat fall off by itself. We could paint epoxy on the areas devoid of gel coat.


After the bottom is cleaned and the loose gel coat removed.

Nellie is doing a good job with the orca impersonation.
After the bottom is cleaned and the loose gel coat removed.
Nellie is doing a good job with the orca impersonation.
Sunday, October 2, 2011
Real Big Bottom Growth
Nellie gets a sea trail of her her new tanks and exhaust system during today's 4.5 hour ride down to Phil Jones' yard on Hopper's Island. The purpose of the haul is to check the bottom, the cutlass bearing and the rudder shaft's packing glad. Nellie's underwater gel coat has been peeling off since before we bought her. Since there are no blisters in the fiberglass the approach has been to let nature take her course. One problem is that when the gel coat falls off it takes the bottom paint with it and thus we're subject to pretty fast flora and fauna growth rates.

Hard to believe but the bottom was last cleaned in May '11. It doesn't help that when the gel coat falls off it takes the bottom paint with it leaving the exposed fiberglass undefended against growth.

This closeup shows barnacles getting under the gel coat. The barnacles are actually doing us a favor by expediting the gel coat's demise. The sooner the gel coat is all off, the sooner we can epoxy the bottom and then barrier coat (Interlux 2000) it.
Hard to believe but the bottom was last cleaned in May '11. It doesn't help that when the gel coat falls off it takes the bottom paint with it leaving the exposed fiberglass undefended against growth.
This closeup shows barnacles getting under the gel coat. The barnacles are actually doing us a favor by expediting the gel coat's demise. The sooner the gel coat is all off, the sooner we can epoxy the bottom and then barrier coat (Interlux 2000) it.
Tuesday, September 27, 2011
We Have Ignition
Houston, we have ignition! After putting 50 gallons in the port aft tank and priming the fuel lines, Nellie started right away. I looked everywhere and found no fuel or raw water leaks--this was the first test of the new exhaust hose too. The Webasto heater, which needs to pull fuel out of the new tanks, worked too. Lowering the height of the tanks by 1/2" wasn't enough to make the existing vent system work. Same problem as before--the tanks' vents are higher than the bottom of the joists.

Since the vent tube must go under the joist and then rise to the tank, this violates the rule that 'the vent tube continuously run downwards'. The pictures below show a way to mitigate the problem. The good news is that drowned vents only effect re-fueling operations, thus the vent line would only need to be cleared prior to refueling.
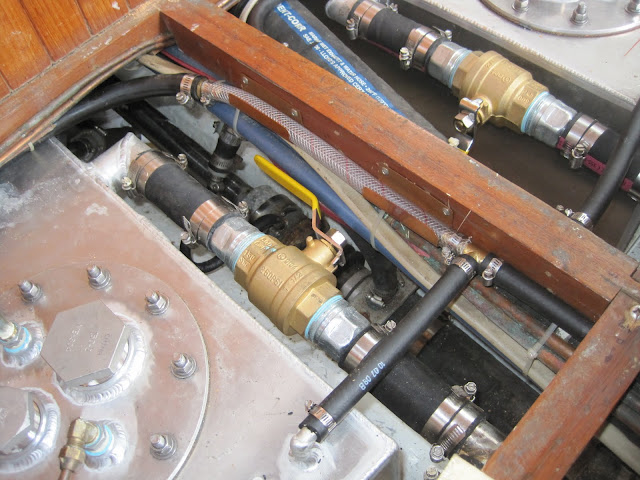
The vent tube attaches to the top of the tank in the bottom center of this photo. The tube then travels inboard to a 'T'. The right leg of the 'T' goes to the aft tank. The left leg, composed partially of semi-transparent tubing, goes to the cabin-side fitting. The semi-transparent tube rides in copper saddles and will be filled with diesel if the vent is flooded.
A flooded vent can be cleared by lowering the 'T' while raising the other end. Then the 'T' is raised and the fuel drains back into the tank.

What a mess. Time to clean up!
Since the vent tube must go under the joist and then rise to the tank, this violates the rule that 'the vent tube continuously run downwards'. The pictures below show a way to mitigate the problem. The good news is that drowned vents only effect re-fueling operations, thus the vent line would only need to be cleared prior to refueling.
The vent tube attaches to the top of the tank in the bottom center of this photo. The tube then travels inboard to a 'T'. The right leg of the 'T' goes to the aft tank. The left leg, composed partially of semi-transparent tubing, goes to the cabin-side fitting. The semi-transparent tube rides in copper saddles and will be filled with diesel if the vent is flooded.
A flooded vent can be cleared by lowering the 'T' while raising the other end. Then the 'T' is raised and the fuel drains back into the tank.
What a mess. Time to clean up!
Monday, September 26, 2011
Tanks are Almost Done
Almost done!
Only the clean-up remains to be done. |
The bilge is less cluttered now. |
Sunday, September 25, 2011
More Tank Plumbing
Finished up installing the fuel supply and return lines.
I thought the floor joists were made of teak. However, after installing bigger fasteners in them today, I believe that the wood is what Tommy Chen calls 'Iron Wood'. We know this wood was used as coring for the fiberglassed floor joist stringer and to make the cradles in which the tugs were shipped to the U.S. Iron Wood is very dense and strong. To hold the joists together the factory used 2" #12 ss screws. Many of the screws were damaged when I removed them. To keep this from happening again, and to beef-up the joint, I re-bored and then countersunk for 2" #8 ss screws. The joists definitely feel more secure now.
The main reason the 3" exhaust hose had to be replaced was because it rotted where it sat in the lazarette-fed bilge area. Originally the factory secured the exhaust hose to the underside of the floor joists with hose clamps. Several of those clamps were missing and thus Nellie's exhaust hose had dipped down. Now the exhaust hose is supported every 20"; high, dry and protected from vibration.
I thought the floor joists were made of teak. However, after installing bigger fasteners in them today, I believe that the wood is what Tommy Chen calls 'Iron Wood'. We know this wood was used as coring for the fiberglassed floor joist stringer and to make the cradles in which the tugs were shipped to the U.S. Iron Wood is very dense and strong. To hold the joists together the factory used 2" #12 ss screws. Many of the screws were damaged when I removed them. To keep this from happening again, and to beef-up the joint, I re-bored and then countersunk for 2" #8 ss screws. The joists definitely feel more secure now.
The main reason the 3" exhaust hose had to be replaced was because it rotted where it sat in the lazarette-fed bilge area. Originally the factory secured the exhaust hose to the underside of the floor joists with hose clamps. Several of those clamps were missing and thus Nellie's exhaust hose had dipped down. Now the exhaust hose is supported every 20"; high, dry and protected from vibration.
Saturday, September 24, 2011
Plumbing the New Tanks
It seems that industry has decided that 1/4" and 3/8" tube is adequate for most jobs, thus 5/16" fittings are hard to come by. What is available seems targeted at repairs and not new-builds. Thus I had to use two ells which are 5/16" ferrule to 1/4" male-NPT instead of 5/16 flared tube to 3/8" male-NPT. I bring this up only because I thought I preferred tube fittings. They're easy to form in the field and are reliable. The ferrule fitting however means you don't have to flare the tube, thus it's faster.
Stainless steel fittings were used to isolate the copper fittings from the aluminum tanks. Another choice could have been nylon fittings. They would sit lower than the stainless fittings and would be self-sealing. I put both nylon tape and pipe dope on all the metal fittings. The problem with nylon fittings is that the USCG doesn't approve it for a commercial vessel. So the question is would Nellie ever become a commercial vessel?
The original manifold is in place. The copper fuel supply and return lines are too.
Thursday, September 22, 2011
In Go the Last Two Tanks
The last two tanks were put in place today. The floor joists were put back too. The new tanks each have a ball valve on the fill line. These were installed and all the new 1-1/2" fuel hose too. The USCG approved hose is expensive stuff at $9/ft. Nellie needed 17.5 feet.
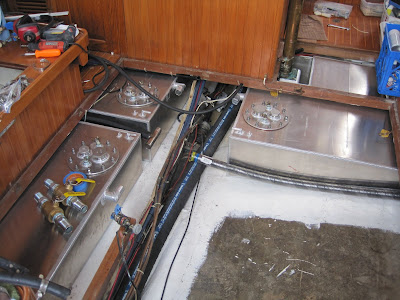
Tank 3, the starboard forward, went in without problems.
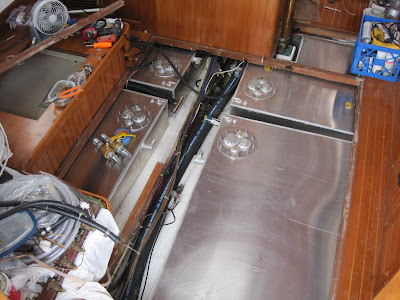
Tank 4, the starboard aft, finds its home ok too.
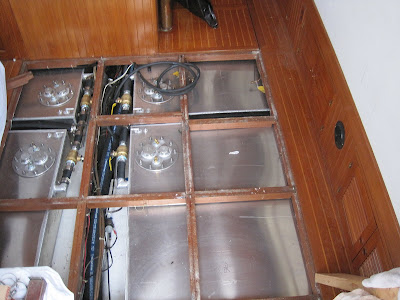
The floor joists going back into place and the fuel filler hoses too. Note the new ball valves for each tank.
Tank 3, the starboard forward, went in without problems.
Tank 4, the starboard aft, finds its home ok too.
The floor joists going back into place and the fuel filler hoses too. Note the new ball valves for each tank.
Wednesday, September 21, 2011
Next Tanks Go In
The port aft tank went in a lot easier than the port forward tank. When cutting the old fuel line off the port deck fill I found evidence of water getting below decks via the fill plate. It'll have to be re-bedded. Getting the fuel tank vent line to run continuously upwards is proving to be difficult. The problem is that the line pierces the deck a long way from the tanks. It then tries to run just under and parallel to the deck until it gets to the tanks. The problem is that the vent line bobs up and down as it spans the rafters. Any fuel finding its way into one of the low spots will get trapped.

Tank 2, the port aft, getting ready to go in.

Tank 2, the port aft, just begining to be slid under all the hoses and wires before it goes under the settee.

The only way to remove the 24 year old fuel line from the fitting is to cut it off. A Dremel tool works wonders.
Tank 2, the port aft, getting ready to go in.
Tank 2, the port aft, just begining to be slid under all the hoses and wires before it goes under the settee.
The only way to remove the 24 year old fuel line from the fitting is to cut it off. A Dremel tool works wonders.
Tuesday, September 20, 2011
Port Forward Fuel Tank Goes In
Lots of rewiring today. Actually, it's mostly just cleaning up wires that are already there. Got the the new port forward fuel tank in. Sure glad the height of the tank was reduced by 1/2". Even so, had to use the hydraulic jack on the settee.
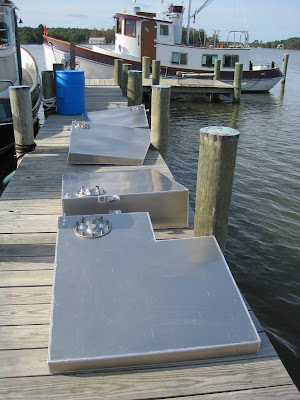
The new tanks are delivered to the dock. Now just installation remains …
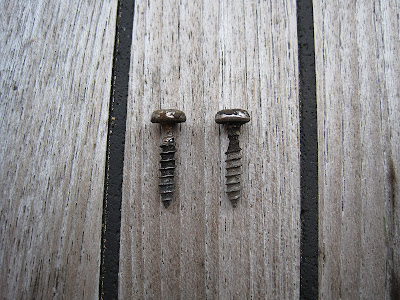
These stainless screws were holding the bilge pump down. Note how the bilge water has eaten them away. The head of the screw was tight against the plastic pump case. The water trapped below it was probably stagnant and stainless will corrode badly in deoxygenated water.

The port forward fuel tank is back in place.
The new tanks are delivered to the dock. Now just installation remains …
These stainless screws were holding the bilge pump down. Note how the bilge water has eaten them away. The head of the screw was tight against the plastic pump case. The water trapped below it was probably stagnant and stainless will corrode badly in deoxygenated water.
The port forward fuel tank is back in place.
Monday, September 19, 2011
Fuel Tank Vent Blockage
The port vent line had a low point (i.e. p-trap) where it penetrated into the bilge. Drilled 3/16" holes in the floor joists and then nylon-tied the 3/4" vent hose tightly to the bottom of the joist. Had to replace the 1100 gpm main bilge pump as one of the plastic tabs which held it into the strainer had broken off.
Saturday, September 10, 2011
Port Bulwark is Retaining Water
Good news. Rebedding the starboard fuel fill plate worked as no water is leaking by it. The port bulwark is getting water inside it. Probably via the hawse pipe to bulwark joint. The water is then dripping below decks via a pinhole leak in the fiberglass. The pinhole leak is 3" outboard of the port fuel fill.
Thursday, August 18, 2011
Fuel Filler Ports--Bad Location
I replaced the 1-1/2" manual bilge pump hose today and was pleasantly surprised that it wasn't all that hard to get to. Also replaced the 1-1/8" aft bilge pump hose. Pulled the fuel filler hoses off too, or more accurately had to use a Dremel tool to cut through the hose where it attached to the filler neck. Tried a heat gun first without success. Those hoses have tenacious holding power. The fuel filler port on the starboard side was the source of water getting below deck. The yard couldn't have put the filler ports in a worse spot—essentially the deck's low point. Water from both the bow and stern run towards the filler port. I couldn't tell if the water was getting by the joint between the filler port and teak, or the joint between the teak and fiberglass. It was obvious when I pressed down on the area around the filler port that water was under the teak deck. Re-bedded and painted the starboard side fuel filler port.
Wednesday, August 17, 2011
Fuel Deck Fill Re-Bed
Removed the port side fuel deck fill and re-bedded it. Removed the 1-1/8" x 11' hose from the aft bilge pump. Removed the 1-1/2" x 4' hose from the manual bilge pump. Andy Bloodsworth finished building the port forward fuel tank.
Monday, August 15, 2011
Sunday, August 14, 2011
Saturday, August 13, 2011
Bilgekote One
Started painting the bilge in salon and galley with bright white Interlux Bilgekote.
Friday, August 12, 2011
Yet Even More Cetol
Second Cetol coat on pilothouse roof trim.
Thursday, August 11, 2011
And More Cetol
First Cetol coat in pilothouse roof trim.
Friday, August 5, 2011
More Cetol and Mast Hardware Repositioning
The last coat of Cetol went on the mast today. Reinstalled the hardware. Moved the halyard's cleat to the starboard side of the mast. This will make it easier to lower and raise the mast as all the hardware to do so is now on the same side.
Thursday, August 4, 2011
More Cetol on Mast
Coat two of Cetol on mast.
Wednesday, August 3, 2011
Lots of Bungs Go Into the Mast
Removed all the mast's hardware and bunged the holes for the hardware not going back on. Sanded the mast back to bare wood. Put the first coat of Cetol on.
Friday, July 15, 2011
Pretty in Red
The freshly painted tiller went back in this morning with two new 3/8" stainless bolts. I'm glad I spent the time getting the tiller off because when Phil Jones' guys at the yard go to replace the rudder shaft's 3", packing gland, support hose, they won't have to spend a bunch of time breaking the tiller free—and it looks good in red ;-)

A freshly painted tiller.

A freshly painted tiller.
Thursday, July 14, 2011
Tiller Removal
Removed the tiller so the scale (rust) could be ground off and then repainted. Clearly it had been awhile since the tiller was last removed. One of the two stainless bolts refused to budge and so had to be cut off.
Tuesday, July 12, 2011
What Supports the Floor?
Got 60+ bungs into the mast. Amazing how many holes one sail track can create.
So, what does support the 13/16" thick floor boards? In a nutshell, floor joists. The joists are 2" thick by 1-3/4" wide. There's a stringer, fiberglassed into the hull, upon which the joists, running athwart, rest upon. The joists are fixed to the stringer by fiberglass.

Looking forward and outboard on the starboard side. The stainless water tank is forward.

Looking outboard at the floor support structure. Starting at the bottom are: (1) turn of the bilge for the fiberglass hull; (2) a stringer fiberglassed to the hull; (3) a floor joist that has been fiberglassed to both the stringer and the hull; and (4) a fixed portion of the floor.
So, what does support the 13/16" thick floor boards? In a nutshell, floor joists. The joists are 2" thick by 1-3/4" wide. There's a stringer, fiberglassed into the hull, upon which the joists, running athwart, rest upon. The joists are fixed to the stringer by fiberglass.

Looking forward and outboard on the starboard side. The stainless water tank is forward.

Looking outboard at the floor support structure. Starting at the bottom are: (1) turn of the bilge for the fiberglass hull; (2) a stringer fiberglassed to the hull; (3) a floor joist that has been fiberglassed to both the stringer and the hull; and (4) a fixed portion of the floor.
Sunday, July 10, 2011
Paint, Hose and Bung
Reinstall the newly painted linear actuator bracket.
Cut the new exhaust hose to length and installed it on the wet muffler.
Put the last remaining bung into the deck.
Attempted to remove the ferrous arms off the rudder shaft. Unable to move the bolts so wet them down with a penetrating oil and will try again tomorrow.

There's severe poultice corrosion occurring under this aluminum Raymarine linear actuator mount. This is happening because the wood, underneath the mount, is hygroscopic, i.e. absorbs moisture. The corrosion is easily eliminated by placing a non-hydroscopic substance between the aluminum and wood. I simply elevated the mount above the wood by using stainless washers.

In the bilge looking aft. The bellows for the PSS can be see at the top of the photo. The prop shaft's intermediary support, with the green patina, is right behind it. There appears to be nothing wrong with the hose connecting the stern tube to the intermediary support. But, with the fuel tanks out it's an easier job to replace it. As evidenced by all the muck in this area of the bilge, it's very hard to get to.
Cut the new exhaust hose to length and installed it on the wet muffler.
Put the last remaining bung into the deck.
Attempted to remove the ferrous arms off the rudder shaft. Unable to move the bolts so wet them down with a penetrating oil and will try again tomorrow.
There's severe poultice corrosion occurring under this aluminum Raymarine linear actuator mount. This is happening because the wood, underneath the mount, is hygroscopic, i.e. absorbs moisture. The corrosion is easily eliminated by placing a non-hydroscopic substance between the aluminum and wood. I simply elevated the mount above the wood by using stainless washers.
In the bilge looking aft. The bellows for the PSS can be see at the top of the photo. The prop shaft's intermediary support, with the green patina, is right behind it. There appears to be nothing wrong with the hose connecting the stern tube to the intermediary support. But, with the fuel tanks out it's an easier job to replace it. As evidenced by all the muck in this area of the bilge, it's very hard to get to.
Saturday, July 9, 2011
Getting the New 3" Exhaust Hose In
Nellie's new 3" wet exhaust hose is in! Removing the Webasto exhaust line, the wet exhaust's 3" through-hull fitting, the linear actuator and its wood support, then soaping the fiberglass inside the bulwark did the trick. However, using Trident Corrugated #252 hose, which bends fairly easily, was the answer. It's interesting that the 'loop' area, which is behind the stern's bulwark, has several spots which are too narrow for the exhaust host to fit. Naturally when the hose tries to enter such an area it merely jams. I used a 1' section of the old hose to probe the route for the new hose. Knowing where the 'shallow waters' were really helped. Removing the wet exhaust's through-hull helped in two ways: (1) gave me better physical access to the 'loop' area; and (2) with the new hose in place it's easy to put 5200 on the through-hull's hull mating surface, twist the through-hull onto the hose, and then manhandle the through-hull into its hole.

Removing the wet exhaust thru-hull made it easier to get the thru-hull into the new hose. Only then was the thru-hull reinstalled into the hull.

With the wet exhaust thru-hull out, hull thickness in this part of the transom measures about 7/16".
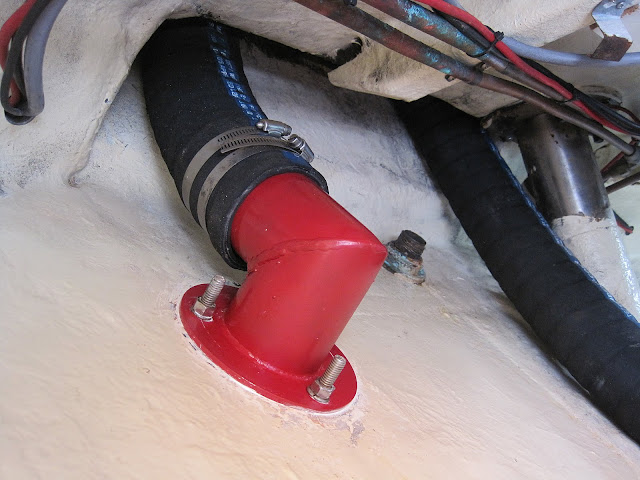
The new hose in place on the freshly painted thru-hull.
Removing the wet exhaust thru-hull made it easier to get the thru-hull into the new hose. Only then was the thru-hull reinstalled into the hull.
With the wet exhaust thru-hull out, hull thickness in this part of the transom measures about 7/16".
The new hose in place on the freshly painted thru-hull.
Thursday, July 7, 2011
Replacing Teak Deck Screws with Dowels
Finished the deck repair. In all 150 screws were replaced with dowels. One deck board under the port forward cabin window had warped upwards. It was successfully clamped flush to the deck and its failed screw replaced with a dowel.
Wednesday, July 6, 2011
Dowels vs Screws to Hold Deck Down
Repaired all the missing bungs on the stern and starboard side. The process is (1) remove the stainless screw (I use a power screwdriver but will revert to doing it by hand if the screw starts to strip out. Doing it this way only 2 out of 150 screws had to be slotted with a Dremel tool before removal); (2) drill out the screw hole its entire length (about 3/4") using a 1/4" twist bit; (3) using a toothpick coat the inside and bottom of the hole with epoxy; (4) roll the dowel in epoxy to cover its sides and bottom; (5) hammer in 1/4" x 3/4" dowel; and finally (6) Using a random orbital sander with 60 or 80 grit (it's best if the sand paper doesn't have the dust pickup holes as the dowels just love to get into the holes and rip the sand paper) sand the dowel flush with the deck before the epoxy dries so that the sawdust is mixed with the wet epoxy forced into any gaps.
Tuesday, July 5, 2011
New, 1/8" Thick, 5250 Aluminum Fuel Tanks -- $3,400
Got a $3400 fuel tank bid from Andy Bloodsworth, using 1/8" 5250, or $137 more per tank using 3/16" 5202. He estimated 6 '4x'10 sheets of aluminum at $200/sheet. Asked him to bid with A36 14 ga mild steel too.
Thursday, June 30, 2011
New 3" Trident #252 Exhaust Host
With good reason it seems I dreaded removing the wet exhaust hose. Resorting to a to grinder with a cutoff wheel isn't exactly an elegant solution. The replacement will have to be more flexible than the old hose. 23' of Trident Corrugated #252 seems to fit the bill.
After leaving the through-hull the exhaust hose loops up into the bulwark before going forward to the wet muffler. |
After 24 years the hose has become very stiff. To try and extract it I pushed up on the hose's near side while pulling down on the rope attached to the far side. |
Looking up into the void. This shot was taken after the hose refused to move any farther. The fiberglass is narrower in the center section and the hose is pinched in place. |
After the hose jammed at the top of the loop, a grinder made the 'extraction' easier albeit messier. |
Wednesday, June 29, 2011
LNVT Fuel Tanks
Got a $3,550 quote from Luther's, Bristol, RI, for the four tanks made of 1/8" 5052 aluminum. Bud Luther, who built Sally W's tanks, redesigned them to be easier to make and also reduced each tank's height by 1/2". Some of this 1/2" space will be used by plastic strips attached to the bottom of the tanks; the idea being to keep the aluminum away from any water.
The LNVTs original mild steel tanks are 14ga or .0747" thick. Aluminum weighs 1/3 as much as steel. So, tanks made from 1/8" aluminum weigh 44% less than those made of 14ga mild steel. Similarly, a tank made of 3/16" aluminum would weigh 16% less than if made from 14ga mild steel. 3/16" aluminum is about four times the price of 14 ga mild steel.
The LNVTs original mild steel tanks are 14ga or .0747" thick. Aluminum weighs 1/3 as much as steel. So, tanks made from 1/8" aluminum weigh 44% less than those made of 14ga mild steel. Similarly, a tank made of 3/16" aluminum would weigh 16% less than if made from 14ga mild steel. 3/16" aluminum is about four times the price of 14 ga mild steel.
A tooth pick marks the hole. At the point of failure corrosion is evident both inside and outside the tank. |
The location of the leak became obvious after pressurizing the aft port tank to 3 psi. |
Monday, June 27, 2011
It took 13.5 Hours To Remove the Fuel Tanks
The last fuel tank, port forward, came out today. It was the most difficult to extract for several reasons: it's under the settee and galley cabinet; the fixed-sole extends over the port tanks more than the starboard; this tank has the most floor joists bearing on it—therefore it's the tightest fit; and, the fiber-glassed-in packing gland support gets in the way. I'd been warned by Allan Seymour, Sally W. (42), that this might happen. The yard took his support out and all the fiberglass grinding left quite a mess. The tank, which must be brought aft and then slid athwart into the Starboard aft tanks old slot, jams under the settee. I used a hydraulic car jack to lift the settee. With the settee elevated a little the tank was worked aft until it's forward inboard edge cleared the bearing.
There is lots of rust on this tank but its confined to specific areas. As with the other tanks the worst spot is along the length of the fiberglass band used to hold the in. There were three rusted regions on the tank's top: under the refrig; under the galley window; and under the middle window.
3:54 hours labor today and 13:29 hours to remove the fuel tanks.
There is lots of rust on this tank but its confined to specific areas. As with the other tanks the worst spot is along the length of the fiberglass band used to hold the in. There were three rusted regions on the tank's top: under the refrig; under the galley window; and under the middle window.
3:54 hours labor today and 13:29 hours to remove the fuel tanks.
Saturday, June 25, 2011
Use Tide to Degrease a Fuel Tank
With a neighbor's help the aft port fuel tank is off the boat.
John Olsen, S/V Daydreamer, recommends using Tide to clean out the tanks—that's what he used in the Alaskan oil patch. John also noted that if aluminum tanks are used, the LNVTs copper fuel lines and manifold can still be used but a stainless fitting will needed to be used to prevent any direct copper-to-aluminum connections. Aluminum tanks would indeed be lighter as mild steel is three times heavier than aluminum. Need to pressure check the repaired tanks (at no more than 3 psi).
1:00 hours labor today and 6:45 hours to date
John Olsen, S/V Daydreamer, recommends using Tide to clean out the tanks—that's what he used in the Alaskan oil patch. John also noted that if aluminum tanks are used, the LNVTs copper fuel lines and manifold can still be used but a stainless fitting will needed to be used to prevent any direct copper-to-aluminum connections. Aluminum tanks would indeed be lighter as mild steel is three times heavier than aluminum. Need to pressure check the repaired tanks (at no more than 3 psi).
1:00 hours labor today and 6:45 hours to date
Friday, June 24, 2011
Fuel Tank Removal Day #2
Fuel tank replacement project day #2. Using a vibratory cutter (like the Fein Multimaster) it took about 50 minutes to cut the fiberglass away from the tank. Once free the tank slid inboard pretty easily. The exhaust hose makes it impossible to get the tank out. Removing the exhaust hose from the muffler and then running it along the starboard cabinets means there's room to get the tank out. Noticed some small cracks along the top of the exhaust hose but underneath was some major damage. It'll have to be replaced.
Things needed:
After a total of 2:00 hours work today, and 4:40 hours total, the starboard aft tank is out. Bicki and I were able to muscle it onto the stern and then with a friend's help we got it off the boat. So far moving the tanks off the boat has been the hardest part of the job.
After another 0:55 hours, mostly to cut the fiberglass and reroute some wires, the aft port tank is free and now sits in the space once occupied by the aft starboard tank.
3:05 hours labor today and 5:45 hours to date.
Things needed:
- 23' of 3" I.D. Marine Exhaust Hose
- 17.5' of 1.5" I.D. Marine Fuel Hose (from deck plates to tanks)
After a total of 2:00 hours work today, and 4:40 hours total, the starboard aft tank is out. Bicki and I were able to muscle it onto the stern and then with a friend's help we got it off the boat. So far moving the tanks off the boat has been the hardest part of the job.
After another 0:55 hours, mostly to cut the fiberglass and reroute some wires, the aft port tank is free and now sits in the space once occupied by the aft starboard tank.
3:05 hours labor today and 5:45 hours to date.
Just as Tommie Chen said, the tanks can be removed |
With the fiberglass removed it's obvious that there was some corrosion going on here |
The aft port tank after it has been moved into the already removed aft starboard tank's space. It's ready to be stood on edge and moved off the boat |
Thursday, June 23, 2011
Fuel Tank Removal Day #1
Fuel tank replacement project day #1. To help others in the fleet I'll keep track of the labor hours it takes to do this project. The stern two tanks are already empty of fuel. Step one is to pull up the floor boards. I've got a feeling this project will breed many others as all ready I can see that the sound dampening insulation under the floor boards can use some work. Next the floor joists are removed. The Phillips stainless screws holding the joists down strip-out easily. I used a Dremel tool with a small grinding wheel to cut a slot into several of the screws. Two of the joists couldn't be removed at all; one goes under the refrigerator while the other goes under the settee. If necessary they can be cut, but I think the tanks will slide under them. In two places wood blocks were wedged between a joist and a fuel tank. The blocks were of different thicknesses and it appears Ocean Eagle Yachts used these to level out the floor. Fuel lines were removed next.
Some thoughts: The least risk approach for tank replacement is not to start over with a new material and installation method, but to build on the 25+ year history. In fact, by repeating what worked and striving to eliminate the causes of the exterior tank corrosion, there's reason to believe the tanks will last longer than 25 years. Here's how I think our tanks are failing, water leaking by a deck fastener, because the fastener missed the deck batten, is getting beneath the tank and then pooling behind the fiberglass tab holding the tank in place.
2:40 hours labor today and 2:40 hours to date.

The Multimaster is the right tool to cut the fiberglass away from the tanks.
The wet exhaust hose is up tight against the aft starboard tank. It will be disconnected from the muffler and moved out of the way.
Picture of the salon looking aft. All the floor boards are removed and a few of the joists too.
Some thoughts: The least risk approach for tank replacement is not to start over with a new material and installation method, but to build on the 25+ year history. In fact, by repeating what worked and striving to eliminate the causes of the exterior tank corrosion, there's reason to believe the tanks will last longer than 25 years. Here's how I think our tanks are failing, water leaking by a deck fastener, because the fastener missed the deck batten, is getting beneath the tank and then pooling behind the fiberglass tab holding the tank in place.
2:40 hours labor today and 2:40 hours to date.
The Multimaster is the right tool to cut the fiberglass away from the tanks.
The wet exhaust hose is up tight against the aft starboard tank. It will be disconnected from the muffler and moved out of the way.
Picture of the salon looking aft. All the floor boards are removed and a few of the joists too.
Friday, June 17, 2011
Balmar ARS-5 Smart Regulator Replacement
Replaced the Balmar ARS-5 alternator regulator with a new one. The old one's potting had cracked and Balmar gave us an RMA for a replacement. When the replacement comes it'll be kept aboard for a spare.
Saturday, May 14, 2011
Bulbs, Batteries and Filters
Installed new spreader light bulbs. Charged the dinks battery and installed new connectors for the dinks sounder to battery connection. Installed new 2 Micron Racor filters and Cummins diesel filter. Sewed up screens for the pilothouses' two opening front windows.
Friday, May 13, 2011
Raw Water Impeller Self Destructs
New dodger. New impeller in both the Cummins and Onan. The Onan's impeller had completely disintegrated while the Cummins' was missing five of its vanes. Had to flush the raw water backwards to get the three pieces lodged against the oil cooler out. Rotated the downstairs AC unit. Much better air flow.
Thursday, May 12, 2011
Use GE SSG4000 to Bed Plexiglass into Stainless
Put new plexiglass on the stateroom's overhead hatch. Bedded the plexiglass in GE SSG4000 as recommended by the Piedmont Plastics, Ft Lauderdale. Time will tell if this product will work. A better and much more expensive choice would have been Sika 226 Cleaner, Sika 209 primer, Sikaflex 295UV Black. These Sika products are universally recommended but together cost $80 as compared to $15 for the SSG4000. Degreased the engine room and bilge.
Update: 22 May 2014--the SSG400 has really held up. Not a single leak. Highly recommend it.
Update: 22 May 2014--the SSG400 has really held up. Not a single leak. Highly recommend it.
Wednesday, May 11, 2011
Stern Light Relocated
Relocated the stern light about 8" higher so it's not hitting the dodger.
Relocated the stern light about 8" higher so it's not hitting the dodger.
Tuesday, May 10, 2011
Turbocharger Rebuild +
Rebuilt the Cummins turbocharger, replaced the injection elbow, and installed an Airsep.
Rebuilt the Cummins turbocharger, replaced the injection elbow, and installed an Airsep.
Thursday, May 5, 2011
New Cushions
New cushions for the salon settee and chairs. New cushions for the stateroom chair.
New Saloon Cushions
New cushions for the salon settee and chairs. New cushions for the stateroom chair.
Monday, April 25, 2011
New ICom MXA-5000
Installed new Icom MXA-5000 AIS receiver with integrated antenna splitter.
Removed Nobeltec AIS-100 and yte.com SR-161 antenna splitter.
New ICom MXA-5000 AIS
Installed new Icom MXA-5000 AIS receiver with integrated antenna splitter.
Removed Nobeltec AIS-100 and yte.com SR-161 antenna splitter.
Thursday, April 21, 2011
Zincs
Bottom cleaned by Commercial Diver Services, Ft. Lauderdale.
Replaced rudder zinc.
Hull plate zinc OK - 95% remaining.
Sunday, April 10, 2011
New Autohelm Type 1 Linear Drive
Replaced Autohelm Type 1 Autopilot Linear Drive with new M81130 Raymarine Linear Drive - Type 1. (identical item now under Raymarine brand)
Sunday, April 3, 2011
New PL-259 Connector
Soldered new PL-259 on HF coax to ICOM-7000 in dash (used high power soldering gun - much better!)
Friday, March 4, 2011
MFJ 4416B
Replaced RF feed wire from the Icom AH-4 Antenna Tuner to the antenna.
Added MFJ 4416B DC power booster to insure sufficient voltage to ICOM-7000 while transmitting.
Wednesday, March 2, 2011
Bottom Cleaning
Bottom cleaning at Salty Sam's Marina. Heavy growth on the running gear. Stbd. zinc is 50% gone.
Wednesday, February 16, 2011
Compounded & waxed house (incl. top), pilot house.
Wednesday, January 5, 2011
Re-installed nameboards, repaired faulty DC wire to stbd. running light.
Tuesday, January 4, 2011
Removed Kahlenberg air horn from service; replaced with 12V DC horn mounted in-stack. Replaced upper controller on Magic Chef.
Sunday, January 2, 2011
Removed and Cetoled nameboards. Repainted saloon with white latex.
Subscribe to:
Posts (Atom)