The forward looking camera (with 72 IR LEDs) camera today. It's big but a perfect color match, i.e. the same white, as the dome camera. Here's a drawing of what it will look like. I was concerned the starboard shroud would interfere with the IR camera but the drawing shows it will clear easily. We'll probably see the topping lift in the aft-looking camera but it shouldn't be too bad.
Got the Kahlenberg #116 and #117 whistles plumbed together today. The combined sound is great. I'd thought that valves at each whistle's inlet would be required to 'tune' the circuit. It turns out that leaving each ball valve wide-open is perfectly acceptable. I'm leaving the ball valves in as it allows flexibility. The next job is to pull the stack, mount the compressor and mount the whistles.
With the stack off it'll be easier to clear all the silicone out of the wire chase (the one through the salon ceiling and into the stack). To keep water from leaking into the headliner a fiberglass dam will be built around the penetration.
Thursday, December 26, 2013
Friday, December 13, 2013
Cameras, Whistles, and Bottom Jobs
Starboard and forward view of mast top with cameras |
Removed the four inspection ports from the fuel tanks. Need to cut the existing 2" fuel fill nipple out and replace it with a 2" stainless deck plate. This will make the fuel ports easier to open and the tanks easier to fill. Removed the pencil zinc plug from the Cummins' heat exchanger.
Nellie uses a 1/2" diameter pencil zinc (these zincs have a 5/16" thread to hold the pencil into the plug). Problem is the brass plug accepts zincs with a 3/8" threads. Need to find/make a brass plug (which has 3/4" thread into the heat exchanger) and accepts our 1/2" with the 5/16" thread.
Designing the mount for the rear view camera. Here's a preliminary. Aft of the mast the camera interferes with the topping lift. So this drawing shows the cameras (yea, two cameras—the second being the forward looking IR) mounted outboard and swept aft of the mast. The 1/4" stainless mounting plate is shown above the 'forward view'.
Designing the compressor system for Nellie's new Kahlenberg 117. Easiest solution is if a 120V, 1.5HP, 6 gallon, pancake compressor fits into the stack. Then only a 120V 12-2 would have to be run from the engine room. Fingers crossed.
Saturday, September 14, 2013
Headliner Dimensions and Finish
Nellie's salon headliner is made up of tongue-and-groove boards that are 1-13/16" wide and ?" thick. The wood used, Laban, is clear grained and light in color. Maple is a close grain substitute. Semigloss is the best match for the finish. (Update: According to Tommy Chen the headliner's luster is a result of mixing semigloss and gloss finishes.)
Friday, September 13, 2013
Replacing Deck Bungs Lessons Learned
Replaced 77 missing deck bungs. Several lessons learned: 60 grit on a random-orbital sander will best grind down the protruding dowel and remove the proud polysulfide caulking; sand the dowel before the epoxy dries so the wood dust will fill the gaps between the dowel and the hole.
Sunday, July 7, 2013
Exhaust Mount for Poor Man's Air Conditioning
Made a plexiglass insert for the starboard, forward salon window. The insert has a 4" hole in it to receive the LG air conditioner's exhaust hose. The insert fits into the window channel and is held in place by closing the window against it.
Poor Man's Air Conditiong |
Saturday, June 22, 2013
Prop Shaft Squeal
With my head in the lazarette I can hear a squeal from the prop shaft. It only happens at low RPMs. The cutlass bearing is at least seven years old. Need to give it a good going over when we haul.
The shaft RPM was 717.7 (as measured with the optical tachometer) x 2.57 reduction = 1844 RPM. About what the helm's electronic tach reads.
An IR thermometer on the header tank reads a 180F while the helm's engine temperature reads 190F—about 10F high. I still suspect a bad ground in the helm. Need to run a larger gauge wire.
The shaft RPM was 717.7 (as measured with the optical tachometer) x 2.57 reduction = 1844 RPM. About what the helm's electronic tach reads.
An IR thermometer on the header tank reads a 180F while the helm's engine temperature reads 190F—about 10F high. I still suspect a bad ground in the helm. Need to run a larger gauge wire.
Thursday, June 13, 2013
Oil Change
At 5512hrs changed the oil and oil filter. With 12 quarts in her the dipstick shows on the lower of the two marks.
Baby Gets New Window Screens
![]() |
Nellie's New Screens |
We weren't lucky enough to get factory window screens and it has been a struggle to come up with a good alternative. Particularly irksome are the little ports in the shower, head, and stateroom. An effective and inexpensive solution is to use the port's stainless ring to hold a screen in place (see picture).
The installation process is very straight forward. In fact, the hardest part of the job is removing the stainless ring. It is bedded in polysulfide but will yield with patience. I used a razor knife to cut the joint around the inside of the window. Then working around the inner circumference, with two screwdrivers and a putty knife, I gradually wedged the ring away from the cabin side. Two things to watch-out for, don't scratch the gel coat and don't bend the ring. With the ring off you'll note that the port itself is well bedded. If there are voids in the port's bedding, fix them now as I suggest the ring be reinstalled without bedding—it'll make replacing a damaged screen much easier. Use the ring as a template but cut the screen about 1/4" smaller. A thin layer of silicone caulk will secure the screen to the ring. After the caulk is dry reinstall the ring. As always, make sure to bed the screws.
I used $3 worth of aluminum screen, 18 x 16 mesh, for the four ports. At $60 a better choice might be stainless steel screening. Worth considering too is the size of the mesh. A 20 x 20 mesh will keep no-see-ums out.
Tuesday, May 28, 2013
Lessons Learned on the Injection Pump Rebuild
Nozzle Masters in Orlando, Florida, rebuilt the pump in two days and charged $424. It took another 2-1/2 hours to reinstall the pump, prime the fuel system, and start the engine. In addition to the DIY dollar savings I appreciate how much I learned about the 4BT's entire fuel system—including how to bleed it.
Lessons Learned
Removing and reinstalling the fuel injection pump is well within the reach of the do-it-yourselfer. The order of removal is: (1) the seven fuel lines; (2) the wire attached to the cutoff solenoid; (3) the throttle bracket; (4) the pump support bracket; (5) the three bolts holding the pump to the engine; and (6) the nut and lock washer holding the pump to the gear. It's not necessary to completely remove from the engine the seven rigid fuel lines which connect to the fuel pump. They do have to be given a little play though. For the four rear-facing injector lines this is accomplished by removing the lines' two retaining clamps (mounted on top of the engine).
The fuel line from the filter attaches to the pump in two locations. Simply removing this line's tee fitting will free the pump. Finally, the fuel return line is small enough to be pushed clear after it's unscrewed. After each fuel line was unscrewed from the injection pump its end was sealed, from foreign matter intrusion, with blue tape.
After removing the big plastic cap from the front of the engine, which gives access to the nut and lock washer holding the shaft to the gear, stuff a rag inside the opening to catch any falling nuts or lock washers. Think of this as cheap insurance because if a part does drop inside the engine it'll be a lot of work to get it out. The only special tool needed was a gear puller. I used one but I'll bet tapping on the injector pump's shaft with a brass mallet would be just as effective.
During removal there's no need to lock the pump's drive shaft, as both the Cummins and Lucas manuals call for. Just make sure the engine is not rotated while the injection pump is off or the timing can be messed up. The Cummins has a top dead center (TDC) locking pin located just inboard of the injection pump. I rotated the engine to TDC and pushed the pin in before removing the pump. The pin was left in place until after the pump was reinstalled. Don't forget to withdraw the pin before starting the engine.
With the engine at TDC for cylinder #1 the manual lift pump works, i.e. the engine's lift pump lobe is disengaged.
Bleeding the engine was done by: (1) hand pumping the lift pump; (2) opening the two bolts on the high pressure side, with the engine cranking, until the escaping fuel had no air in it; and, then (3) loosening the fuel line connection at the injector for cylinders 1 & 4. It took about 15 seconds of cranking until the engine started.
The Nozzle Master tech said he likes to advance the pump's timing a little. For the Cummins this is done by rotating the injection pump clockwise (while facing towards the bow). I did not try this but rather used the existing factory timing marks.
Lessons Learned
Removing and reinstalling the fuel injection pump is well within the reach of the do-it-yourselfer. The order of removal is: (1) the seven fuel lines; (2) the wire attached to the cutoff solenoid; (3) the throttle bracket; (4) the pump support bracket; (5) the three bolts holding the pump to the engine; and (6) the nut and lock washer holding the pump to the gear. It's not necessary to completely remove from the engine the seven rigid fuel lines which connect to the fuel pump. They do have to be given a little play though. For the four rear-facing injector lines this is accomplished by removing the lines' two retaining clamps (mounted on top of the engine).
The fuel line from the filter attaches to the pump in two locations. Simply removing this line's tee fitting will free the pump. Finally, the fuel return line is small enough to be pushed clear after it's unscrewed. After each fuel line was unscrewed from the injection pump its end was sealed, from foreign matter intrusion, with blue tape.
After removing the big plastic cap from the front of the engine, which gives access to the nut and lock washer holding the shaft to the gear, stuff a rag inside the opening to catch any falling nuts or lock washers. Think of this as cheap insurance because if a part does drop inside the engine it'll be a lot of work to get it out. The only special tool needed was a gear puller. I used one but I'll bet tapping on the injector pump's shaft with a brass mallet would be just as effective.
During removal there's no need to lock the pump's drive shaft, as both the Cummins and Lucas manuals call for. Just make sure the engine is not rotated while the injection pump is off or the timing can be messed up. The Cummins has a top dead center (TDC) locking pin located just inboard of the injection pump. I rotated the engine to TDC and pushed the pin in before removing the pump. The pin was left in place until after the pump was reinstalled. Don't forget to withdraw the pin before starting the engine.
With the engine at TDC for cylinder #1 the manual lift pump works, i.e. the engine's lift pump lobe is disengaged.
Bleeding the engine was done by: (1) hand pumping the lift pump; (2) opening the two bolts on the high pressure side, with the engine cranking, until the escaping fuel had no air in it; and, then (3) loosening the fuel line connection at the injector for cylinders 1 & 4. It took about 15 seconds of cranking until the engine started.
The Nozzle Master tech said he likes to advance the pump's timing a little. For the Cummins this is done by rotating the injection pump clockwise (while facing towards the bow). I did not try this but rather used the existing factory timing marks.
Sunday, May 26, 2013
Hmm, Cummins Injector Pump Circling the Drain?
Last week Nellie's fuel injection pump started to leak from the auto advance assembly's gasket. Not a big deal but certainly a warning flag for things to come. After all, its gaskets and seals are 25 years old and have been operated for 5500 hours.
It took three hours today to remove the pump—but much of that was head scratching and looking for the right-sized wrench or socket.
Tuesday, May 21, 2013
Force 10 Stove Fix
The Force 10's biggest burner isn't lighting easily. The tech at Force 10 recommended reseating the thermocouple's retaining nut as this is how it's electrically grounded. The fix worked.
Tuesday, May 14, 2013
Washing Machine's Automatic Cold Water Valve
The clothes washer's hot water valve is not opening all the way which makes filling the washer with water a bloody long process. The washer fills fine with the cold water valve alone. Replace the hot water valve.
Friday, May 3, 2013
Replacing the Windshield Wipers
Replaced the 16" windshield wipers with 17" ones. They fit fine. The wiper's bayonet connector is an industry standard. Lubricated the spring mechanism and now the wipers are being held more firmly on the glass. Cleaned the decks with Oxy Clean.
Thursday, May 2, 2013
Galley Headliner Leaks
In the midst of the worst torrential downpours Key West has seen since the 1800's, and they've had a lot of downpours in the intervening years, we get serious about finding the source of the leak(s) in the galley's headliner. We drop seven planks and discover there are actually two leaks. The most water is coming from the wire bundle penetration inside the stack. This will be an easy fix. The second, smaller leak, is just to port of the first but still under the stack. I'll caulk the stack to the pilothouse and also rebed the four stack mounting bolts. The headliner has some water damage but replacing a few planks should take care of that. The trick will be matching the color and grain. Quarter sawn maple is supposed to be a good approximation for the grain.
Saturday, April 27, 2013
Deck Bungs...
Replaced another 39 deck bungs with teak dowel. Used West 205 in lieu of 5 minute epoxy. The bungs need to be sanded down while the epoxy is wet so the saw dust fills any voids. The West is less viscous and some of the bungs rotated while being sanded. This is an atheistic problem as the bung's grain can go out of alignment with the deck's grain.
Thursday, April 25, 2013
HIgh Current Battery Switch and Warm Color LEDs
Replaced the thruster isolation switch with a Blue Seas M-Series 6006. It's rated for 1,500A for 10 seconds, 775A for 60 seconds, 500A intermittent over 5 minutes, and 300A continuously. The thruster draws less than 425A. Definitely don't want to run it continuously for more than 2-1/2 minutes.
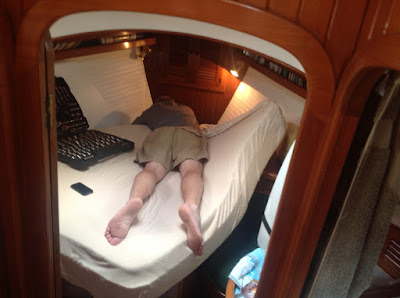
Not a flattering shot but what can you do? Installed a 12 LED, yellow-white light in the existing fixture over the sink. The LED comes with wire leads which easily fit under the socket's retaining screws for the +12 and ground lines. The new LED's light is much warmer than that of the blue-white LED I previously installed. In fact, the yellow-white LED light is very much like that given off by the existing incandescent bulb. The only thing that keeps me from replacing all the incandescent bulbs with LEDs is their $18/each cost. Question is how to keep the incandescent bulbs working continuously, not intermittently as they're prone to now. A Google search is in order.
Not a flattering shot but what can you do? Installed a 12 LED, yellow-white light in the existing fixture over the sink. The LED comes with wire leads which easily fit under the socket's retaining screws for the +12 and ground lines. The new LED's light is much warmer than that of the blue-white LED I previously installed. In fact, the yellow-white LED light is very much like that given off by the existing incandescent bulb. The only thing that keeps me from replacing all the incandescent bulbs with LEDs is their $18/each cost. Question is how to keep the incandescent bulbs working continuously, not intermittently as they're prone to now. A Google search is in order.
Sunday, April 21, 2013
Final Fix On Slipping Simpson Davit Wire Rope
The new wire rope in both davits has come loose from the winch drum's retaining clip. To fix the problem the retaining clip was tightened. Additionally the wire rope's bitter end, after the retaining clip, now goes all the way around the drum and then passes back into it. This extra wrap should keep the wire from slipping. The secret to putting new wire rope on the drum is to remove the three bolts holding the drum to the electric motor. With the drum and electric motor apart, it's much easier to get to the drum's wire rope retaining clip.
Monday, January 14, 2013
Wearing Impeller Pump and Final Head (as in Toilet) Thoughts
Since replacing the impeller the pump has been dripping water. Upon inspection I found two things. First, the pump's wear plate was really worn (was doing it's job I guess). Second, there was no gasket between the wear plate and the engine. I made and installed a gasket, put the worn part of the wear plate against the gasket, put the impeller against the wear plate, and finally the pump housing over the impeller. No leaks. Nellie has a spare raw water pump aboard. When next the impeller is ready to be changed out, I should put the whole spare pump in.
Some final 'head' thoughts: The world has changed and it was while rebuilding Nellie's sanitation system that this point was driven home in some interesting ways. The old sanitation design (see first diagram below) reflected the mores of its time. Nellie's new design (see second diagram below) reflects today's rules and maybe, even some of tomorrow's. Almost everywhere in US waters it's illegal to pump the head directly overboard. In fact, where we normally cruise, the inland waters of the east coast, even having an open head through-hull is a fineable offense. So, how does this affect Nellie's sanitation design? Surprisingly in some dramatic ways, and mostly for the better.


When, by law, a normally-open through-hull becomes normally-closed, it's a game changer. There's a cascading affect on the sanitation system's design. The design used to require an anti-siphon and a three-way valve. The first kept the boat from flooding via the always-open thru-hull. The second allowed toilet waste to bypass the holding tank and go directly to the thru-hull. Now, redesign the system about a closed thru-hull and things get simpler. All toilet waste goes to the holding tank. From there the waste is either pumped overboard or vacuumed out via the foredeck fitting. Here's the up-side: by removing the anti-siphon and the three-way valve we eliminated 30' of hose, a dozen hose clamps, and myriad sources of potential 'stink'. A good trade I think against the ability to flush the head directly overboard. This project also resulted in some interesting lessons learned:
1. The old 3/4" vent line was mostly clogged at its connection to the holding tank. The new vent line slopes upward from the tank fitting so that sloshing effluent will drain back into the tank with enough speed to scrub the line's walls.
2. Don't use brass fitting in a sanitation system—they'll dissolve. Use PVC or nylon.
3. All effluent lines slope towards where they drain to eliminate 'standing' effluent and the resultant odors.
4. The same long-moleculed plasticizer which makes PVC hose flexible also makes it more permeable to odors than solid PVC pipe.
5. A little heat from a heat gun greatly helps get stiff, white PVC hose over a barbed connector.
6. Effluent odors can permeate an inexpensive polyethylene holding tank. Test for this by first cleaning a section of the tank and then wipe the area with a cotton cloth. Take the cloth off the boat and then smell it. If head odor is present the polyethylene tank is permeable.
7. Adding some clear 1-1/2" hose at the through-hull allows you to see when you're done pumping out the holding tank.
8. Hiding the toilets water and effluent lines under the toilet's platform gives a cleaner look to the head. There's plenty of space under the platform to house the lines and it can be accessed from a hole made in either the engine room bulkhead or in the bottom of the stateroom's hanging locker.
In conclusion, new laws, and hopefully some enlightenment, motivated us to change how we operate Nellie's sanitation system. Now all head effluent goes into the holding tank. The holding tank can be emptied with either a shore based pump out or into the surrounding water via a through-hull. Looking to the future, Vermont's law may be an example of what we can expect next—there it's illegal to even have a hose connecting the holding tank to an underwater through-hull. Clearly we haven't gone that far with Nellie but that configuration is achievable by removing just a few hose clamps.
Thanks got to Bob White, Renegade #72, for his review and inputs.
Some final 'head' thoughts: The world has changed and it was while rebuilding Nellie's sanitation system that this point was driven home in some interesting ways. The old sanitation design (see first diagram below) reflected the mores of its time. Nellie's new design (see second diagram below) reflects today's rules and maybe, even some of tomorrow's. Almost everywhere in US waters it's illegal to pump the head directly overboard. In fact, where we normally cruise, the inland waters of the east coast, even having an open head through-hull is a fineable offense. So, how does this affect Nellie's sanitation design? Surprisingly in some dramatic ways, and mostly for the better.


When, by law, a normally-open through-hull becomes normally-closed, it's a game changer. There's a cascading affect on the sanitation system's design. The design used to require an anti-siphon and a three-way valve. The first kept the boat from flooding via the always-open thru-hull. The second allowed toilet waste to bypass the holding tank and go directly to the thru-hull. Now, redesign the system about a closed thru-hull and things get simpler. All toilet waste goes to the holding tank. From there the waste is either pumped overboard or vacuumed out via the foredeck fitting. Here's the up-side: by removing the anti-siphon and the three-way valve we eliminated 30' of hose, a dozen hose clamps, and myriad sources of potential 'stink'. A good trade I think against the ability to flush the head directly overboard. This project also resulted in some interesting lessons learned:
1. The old 3/4" vent line was mostly clogged at its connection to the holding tank. The new vent line slopes upward from the tank fitting so that sloshing effluent will drain back into the tank with enough speed to scrub the line's walls.
2. Don't use brass fitting in a sanitation system—they'll dissolve. Use PVC or nylon.
3. All effluent lines slope towards where they drain to eliminate 'standing' effluent and the resultant odors.
4. The same long-moleculed plasticizer which makes PVC hose flexible also makes it more permeable to odors than solid PVC pipe.
5. A little heat from a heat gun greatly helps get stiff, white PVC hose over a barbed connector.
6. Effluent odors can permeate an inexpensive polyethylene holding tank. Test for this by first cleaning a section of the tank and then wipe the area with a cotton cloth. Take the cloth off the boat and then smell it. If head odor is present the polyethylene tank is permeable.
7. Adding some clear 1-1/2" hose at the through-hull allows you to see when you're done pumping out the holding tank.
8. Hiding the toilets water and effluent lines under the toilet's platform gives a cleaner look to the head. There's plenty of space under the platform to house the lines and it can be accessed from a hole made in either the engine room bulkhead or in the bottom of the stateroom's hanging locker.
In conclusion, new laws, and hopefully some enlightenment, motivated us to change how we operate Nellie's sanitation system. Now all head effluent goes into the holding tank. The holding tank can be emptied with either a shore based pump out or into the surrounding water via a through-hull. Looking to the future, Vermont's law may be an example of what we can expect next—there it's illegal to even have a hose connecting the holding tank to an underwater through-hull. Clearly we haven't gone that far with Nellie but that configuration is achievable by removing just a few hose clamps.
Thanks got to Bob White, Renegade #72, for his review and inputs.
Sunday, January 13, 2013
Replacing Simpson Davit Wire Rope
Put new wire rope (two each 18' of 7x19, right hand lay, 5/32" (4mm), stainless steel), swages, and thimbles in both davits. The 5/32" Amsteel-Blue worked fine but i worried about it chafing. It's now a spare and stored inside the starboard davit.
Thursday, January 10, 2013
Oil Change Kind-of Day
At 5275 engine hours: new Racor and Cummins fuel filters; Cummins oil change and new oil filter; and transmission oil change. At 224 Onan engine hours changed the oil.
Monday, January 7, 2013
Paint and Poly...
Sanded and applied two coats of satin Minwax Polyurethane to the pilot houses' bench seat. Sanded and put one coat of Cetol on the Dutch door jams. Painted the two diesel deck fill plates yellow and two water deck fill plates blue. Painted the 2M and AM/FM antennas white. Wispy fiberglass strands were starting to show on each. Made new fiberglass screens for each small opening port.
Subscribe to:
Posts (Atom)